ecoCasting - sustainable casting processes
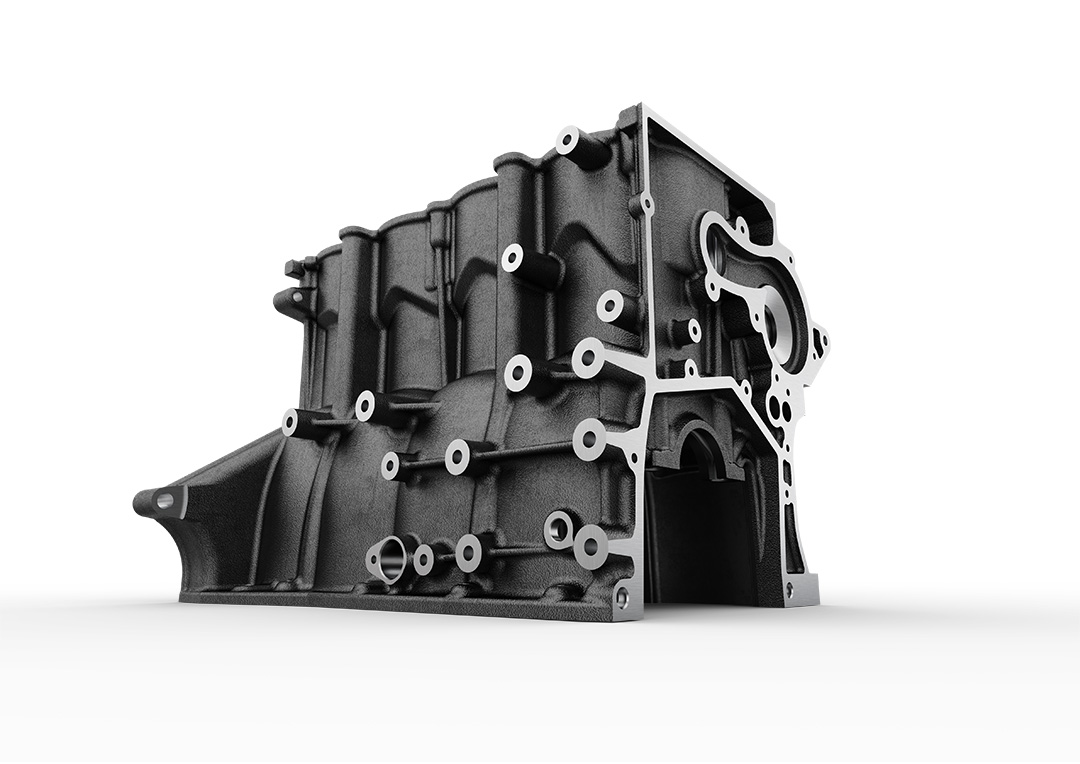
Sustainable passenger car engine blocks with ecoCasting
Engine blocks without aluminum - that's what Fritz Winter developed the ecoCasting process for in 2015. Together with our customers from the global automotive industry, we develop products from 100 percent recycled steel scrap. The process also enables us to produce particularly thin walls and thus lightweight products. The process is also sustainable because, compared to the conventional casting process, we use fewer resources such as water or energy and do not use molding sand. For a detailed overview of the qualitative characteristics of our passenger car engine blocks, please refer to our study: download study.
Cheaper materials
Thanks to standardized but flexible process, you save at least 28 percent of the cost compared to an aluminum cylinder block.
.
Lighter products
We provide sustainable support for the realization of your environmental goals with products that are 30 percent lighter than a conventional gray cast iron cylinder block.
Lower energy consumption
In the production of a ton of cast iron, we need only a fifth of the energy compared to this amount of aluminum.
Precise wall thickness
For engine blocks, every gram counts. The ecoCasting process creates maximum precision and enables wall thicknesses of just 2.5 mm with a tolerance of +/-0.5 mm.
Outstanding quality worldwide
The standardization of our processes, tools and quality management guarantees you a high level of process reliability worldwide - from development to the high-quality product.
Sustainable iron casting process
Thanks to the moldless process, the associated mono-sand system, the closed material cycle and the use of 100 percent steel scrap, we achieve high savings in resources, energy and water.
.
You have questions about our ecoCasting manufacturing process? We will be happy to assist you with your request.